Ensure Quality Control with the Reliable GO NO GO Thread Gauge
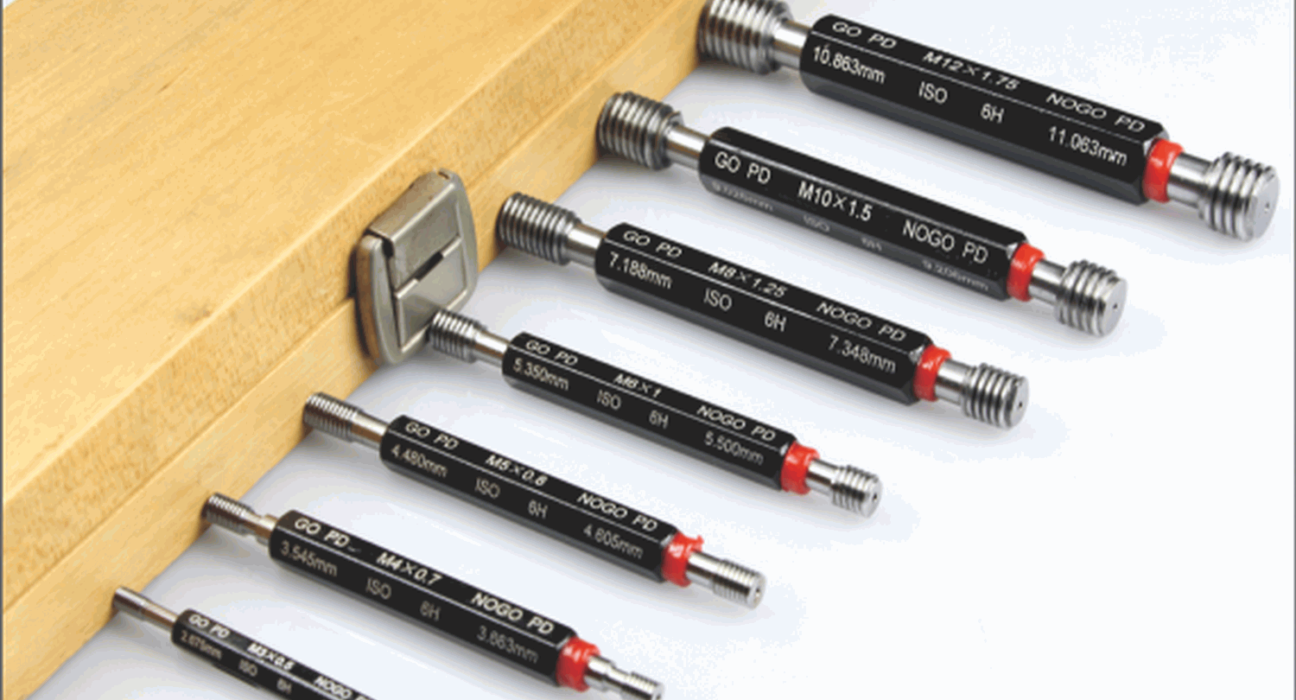
In the realm of precision manufacturing and quality control, ensuring the integrity and accuracy of threaded components is crucial. Whether you’re in aerospace, automotive, or any industry reliant on threaded fasteners, the GO NO GO thread gauge stands as an indispensable tool for maintaining high standards of quality. This article delves into the significance of the GO NO GO thread gauge, its applications, and how it can help you ensure quality control in your manufacturing processes.
Understanding the GO NO GO Thread Gauge
The GO NO GO thread gauge is a fundamental tool used in quality control to measure and validate the dimensions of threaded components. It consists of two distinct gauges: the “GO” gauge and the “NO GO” gauge.
- GO Gauge: This gauge is used to check if the threaded component’s dimensions are within the acceptable range. If the thread fits the GO gauge, it indicates that the component is likely within the correct specifications and can be considered for further processing or assembly.
- NO GO Gauge: The NO GO gauge is designed to ensure that the threaded component does not exceed the maximum permissible size. If the thread fails to fit the NO GO gauge, it indicates that the component is out of tolerance and should not be used.
By employing both gauges, manufacturers can efficiently assess whether a threaded component is fit for use or needs rework, thus ensuring consistency and reliability in their products.
Importance of the GO NO GO Thread Gauge
- Accuracy and Precision: The GO NO GO thread gauge provides a quick and accurate method to verify thread dimensions. Its use minimizes human error and ensures that components meet stringent quality standards.
- Cost Efficiency: Using GO NO GO gauges can help avoid costly rework and scrap by catching defects early in the production process. This not only saves money but also improves overall productivity and reduces waste.
- Compliance with Standards: Many industries have strict standards and regulations regarding thread dimensions. The GO NO GO thread gauge helps ensure compliance with these standards, making it easier to meet industry requirements and avoid penalties.
- Consistency in Production: Regular use of GO NO GO gauges helps maintain consistency across production runs. This consistency is vital for maintaining product quality and reliability, especially in industries where precision is critical.
Applications of the GO NO GO Thread Gauge
The GO NO GO thread gauge finds applications in various industries and scenarios, including:
- Aerospace Industry: In aerospace manufacturing, threaded components must adhere to extremely tight tolerances. GO NO GO gauges help ensure that all components meet these specifications, which is crucial for safety and performance in aerospace applications.
- Automotive Industry: Automotive components often involve complex threaded assemblies. The GO NO GO thread gauge ensures that all threads are within tolerance, helping to avoid issues related to assembly and performance.
- Oil and Gas Industry: Components used in the oil and gas industry must withstand harsh conditions and maintain high reliability. GO NO GO gauges are used to ensure that threaded parts meet the required standards for pressure and durability.
- General Manufacturing: In general manufacturing, the GO NO GO thread gauge is used to ensure that threaded components meet quality standards and are suitable for use in various applications, from machinery to consumer products.
How to Use the GO NO GO Thread Gauge
- Preparation: Before using the GO NO GO thread gauge, ensure that it is clean and free from any debris or damage. Inspect the gauges regularly to maintain their accuracy.
- Measurement: Start by using the GO gauge to check if the threaded component fits properly. If it does, proceed to use the NO GO gauge to ensure the thread does not exceed the maximum permissible size.
- Inspection: Carefully inspect the results. If the component fits the GO gauge but fails the NO GO gauge, it is out of tolerance and should not be used.
- Documentation: Record the results of your measurements to track the quality of your production and identify any trends or issues that may need addressing.
Best Practices for Maintaining GO NO GO Thread Gauges
- Regular Calibration: Periodically calibrate your GO NO GO gauges to ensure their accuracy. Calibration should be performed according to manufacturer recommendations or industry standards.
- Proper Storage: Store gauges in a clean, dry environment to prevent damage and ensure longevity. Use protective cases or covers to shield them from dust and physical impacts.
- Routine Checks: Regularly check the condition of your gauges. Replace any that show signs of wear or damage to maintain consistent measurement accuracy.
- Training: Ensure that personnel using the gauges are properly trained. Proper handling and measurement techniques are essential for maintaining quality control standards.
Conclusion
In the quest for precision and quality in manufacturing, the GO NO GO thread gauge stands as a reliable and indispensable tool. Its ability to ensure that threaded components meet stringent specifications helps prevent costly errors, maintain consistency, and comply with industry standards. By incorporating GO NO GO thread gauges into your quality control processes, you can enhance the accuracy and reliability of your products, ultimately leading to greater customer satisfaction and operational efficiency.
Whether you’re working in aerospace, automotive, or any other industry that relies on threaded components, investing in high-quality GO NO GO gauges and adhering to best practices for their use and maintenance will pay dividends in quality control. Embrace the reliability of the GO NO GO thread gauge and ensure that every component you produce meets the highest standards of precision and performance.