Automated Bulk Handling Systems for Manufacturing Automation: Revolutionizing Efficiency and Productivity
In today’s fast-paced industrial landscape, the demand for faster, more efficient, and cost-effective production processes is ever-increasing. Manufacturing automation has become the cornerstone of industrial innovation, and at the heart of this advancement lies automated bulk handling systems. These systems are transforming how industries manage materials, moving from manual, labor-intensive processes to fully automated solutions that enhance efficiency and productivity.
This blog delves into the significance of automated bulk handling systems, their role in manufacturing automation, and how they are shaping the future of industrial operations.
‣ What Are Automated Bulk Handling Systems?
Automated bulk handling systems are sophisticated machinery and technology designed to handle large volumes of materials—whether solid, liquid, or gaseous—without human intervention. These systems streamline the movement, storage, and processing of bulk materials through conveyors, pneumatic tubes, and robotic arms, among other mechanisms.
By integrating automation technologies like sensors, AI-driven controllers, and machine learning algorithms, these systems can operate 24/7 with minimal human oversight. They are widely used across various industries such as food processing, mining, agriculture, pharmaceuticals, chemicals, and more.
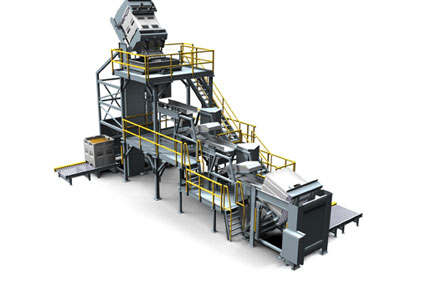
‣ The Importance of Bulk Handling in Manufacturing
Bulk material handling is the foundation of any large-scale production process. It involves the transportation, storage, and control of materials in bulk, ensuring they move efficiently through the production pipeline. Efficient bulk handling is crucial because it can affect production speeds, product quality, and operational costs.
Traditionally, bulk handling was a labor-intensive process, requiring manual work to move materials from one stage of production to the next. However, with the rise of manufacturing automation, businesses can now automate these processes, saving time, reducing labor costs, and minimizing the risk of human error.
‣ How Automated Bulk Handling Systems Enhance Manufacturing Automation
The integration of automated bulk handling systems into manufacturing processes brings a plethora of benefits. Let’s explore how these systems improve manufacturing automation:
1. Increased Efficiency and Throughput
Automated bulk handling systems are designed to operate continuously, which means production lines can run around the clock without the need for breaks or human intervention. This leads to a significant increase in throughput, allowing businesses to meet higher production demands in less time.
2. Cost Reduction
Automation dramatically reduces the need for manual labor, which is one of the largest expenses in manufacturing operations. By implementing automated bulk handling systems, businesses can cut labor costs while also reducing the costs associated with human error, material waste, and equipment downtime.
3. Improved Accuracy and Precision
When handling large quantities of materials, even the smallest error can lead to significant product loss or quality issues. Automated systems use sensors, controllers, and software to precisely control material flow, ensuring accurate quantities are processed at each stage of production. This improves product consistency and reduces waste.
For instance, in the pharmaceutical industry, precision is paramount. Automated bulk handling systems ensure that ingredients are measured and mixed with exacting accuracy, adhering to stringent industry standards.
4. Enhanced Safety
Manual material handling can be dangerous, especially when dealing with hazardous or heavy materials. Automating these processes reduces the risk of workplace accidents and injuries, creating a safer working environment. Automated systems can handle toxic chemicals, flammable materials, or bulky items without putting human workers at risk.
5. Minimised Human Error
Human error is a significant factor in material handling inefficiencies. Mistakes in measurement, transportation, or storage can lead to costly delays and material waste. Automated systems are programmed to follow precise protocols, eliminating the possibility of human error and ensuring that production runs smoothly.
6. Scalability and Flexibility
Automated bulk handling systems offer greater scalability. As production demands increase, these systems can be easily expanded or reconfigured to handle higher volumes of materials. This scalability ensures that businesses can grow without major disruptions to their operations.
Flexibility is another key advantage. Many automated systems can be programmed to handle different types of materials or switch between tasks with minimal downtime, offering versatility in a fast-changing manufacturing environment.
‣ Applications of Automated Bulk Handling Systems in Different Industries
1. Food and Beverage Industry
Automated bulk handling systems are vital in the food and beverage industry, where hygiene and precision are critical. These systems help in the bulk transportation of ingredients, ensuring that they are safely handled and precisely measured to maintain product quality.
2. Pharmaceuticals
In the pharmaceutical industry, bulk handling systems ensure that raw materials such as powders, granules, and liquids are processed accurately. This not only improves production efficiency but also ensures compliance with regulatory standards, as precision is key in pharmaceutical manufacturing.
3. Mining and Quarrying
Bulk material handling is essential in mining and quarrying, where vast quantities of materials need to be transported over long distances. Automated systems can handle tasks such as loading, unloading, and transporting raw materials like coal, ore, and aggregate with minimal human intervention.
4. Chemical Processing
The chemical industry deals with hazardous and sensitive materials that require precise handling. Automated bulk handling systems ensure that these materials are transported and stored safely, reducing the risk of contamination, spills, or exposure to harmful substances.
As automation technology continues to advance, we can expect further innovations in bulk handling systems. The rise of Industry 4.0 and the integration of IoT (Internet of Things) will bring even greater connectivity and intelligence to these systems. Predictive maintenance, AI-driven decision-making, and real-time monitoring are just some of the features that will become more prevalent in future automated bulk handling solutions.
Automated bulk handling systems are revolutionising manufacturing automation, driving efficiency, reducing costs, and improving safety across industries. As technology evolves, these systems will only become more sophisticated, enabling manufacturers to meet growing production demands with greater precision and flexibility. For industries that rely on bulk material handling, adopting automated solutions is no longer just an option—it’s a necessity for staying competitive in the modern industrial landscape. For more information, feel free to check us out.